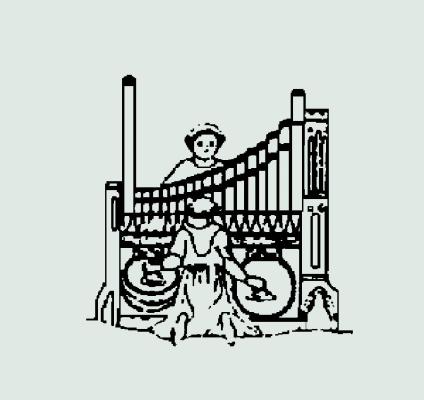
Hemry Pipe Organ Co., Ltd., Novelty, Ohio
St. Joseph Parish, Avon Lake, Ohio
The new organ at St. Joseph’s started life in 1937 as a 17-rank organ for the Cathedral of St. John in Cleveland. It also served in the diocesan St. John College for a number of years until that building was razed in 1980–81. Father John Minnick got wind of the organ’s availability and contracted with our firm to obtain and rebuild the instrument for Holy Trinity Parish in Bedford Heights. The organ was expanded to 36 ranks at the time, utilizing about 12 ranks from the 1937 instrument.
Largely because of demographic considerations, the organ again became available in 1999. Father Tim O’Conner, then pastor of St. Joseph Parish, knowing the qualities of the Bedford organ, acquired the instrument, to be installed one day in the new church sanctuary. The instrument was dismantled and put into storage in various places on the St. Joseph grounds. The heaviest parts (windchests) were actually placed in the balcony while construction was underway in the sanctuary. (Thank you, scissor lifts.)
Over the years, the dream and finances took shape, and eventually, with a contract in the spring of 2014, the final designs were developed and construction began. The instrument is surrounded by new casework of red oak with speaking façade pipes of flamed copper and silver matte-finished zinc. The casework and pipes were expertly executed to our new design by the firm of A. R. Schopp’s Sons in Alliance, Ohio.
The sound resources of the new organ are supplied by pipework from the 1937 and 1981 instruments, with additional pipework for a total of 41 ranks of pipes. Most of the pipework is placed on electric-action slider chests. The organ has two digital stops that provide the deep bass tones heard in the pedal division.
Wind for the pipes is supplied by a 11⁄2 HP blower mounted behind the rear wall of the balcony. A CAT-5 data cable connects the organ’s mechanisms to a three-manual console, which is placed in the balcony opposite from the casework. If desired, it will be possible in the future to connect a second console to the system, to be placed downstairs in the side choir area.
Thanks to the efforts of Father O’Conner and architect Tom Ziska, the room is blessed with very friendly acoustics for organ music, and it is hoped that the instrument, now in its fourth home, will serve the congregation with beautiful musical sounds for many years to come. A special note of gratitude goes to Dave Aslaksen for his help in coordinating various logistical aspects of the storage, construction, and a few needed alterations to the building to accommodate the instrument. Thanks also to Father Ron Wearsch, the present pastor of St. Joseph’s, for continuing this great work that was so ably begun by his predecessor.
Design, construction, and tonal finishing—Tim and Cathy Hemry
Installation and wiring—Kenneth Stenger, Aaron Hemry, Ron Bates
Casework and façade pipework—A. R. Schopp’s Sons, Inc.
Windchests and various components—Organ Supply Industries
Organ control systems—Syndyne Corporation
Digital voices—Integrated Organ Technology Inc.
GREAT
16′ Prestant (digital 1–8)
8′ Principal
8′ Geigen Diapason (Sw)
8′ Chimney Flute
8′ Gamba
4′ Octave
4′ Metal Flute
22⁄3′ Twelfth
2′ Super Octave
V Mixture
8′ Trumpet
8′ Trompeta Real
Great to Great 4
Swell to Great 16-8-4
Positiv to Great 16-8-4
Chimes (digital)
SWELL
8′ Geigen Diapason (1–12, Gt Gamba)
8′ Gemshorn
8′ Voix Celeste FF
8′ Lieblich Gedeckt
4′ Geigen Octave (ext)
4′ Wood Flute
2′ Blockflöte
II Sesquialtera
III Mixture
16′ Fagotto
8′ Fagotto (ext)
8′ Hautbois
4′ Fagotto (ext)
Tremulant
8′ Trompeta Real (Gt)
Swell to Swell 16-UO-4
Harp (digital)
POSITIV
8′ Gedeckt
8′ Gamba (Gt)
4′ Chimney Flute
4′ Gamba (ext)
2′ Principal
11⁄3′ Quinte
III Cymbal
8′ Clarinet
8′ Trumpet (Gt)
Tremulant
8′ Trompeta Real (Gt)
Swell to Positiv 16-8-4
Cymbal Bells
Great/Positiv Reverse
PEDAL
32′ Bourdon (digital)
16′ Prestant (Gt)
16′ Metal Gedeckt
16′ Bourdon (digital)
8′ Diapason
8′ Geigen (Sw)
8′ Gamba (Gt)
8′ Flute
4′ Gamba (Gt)
II Choralbass
32′ Trombone (digital)
16′ Contra Trumpet (ext, Gt)
16′ Fagotto (Sw)
8′ Trumpet (Gt)
4′ Fagotto (Sw)
8′ Trompeta Real (Gt)
Great to Pedal 8
Swell to Pedal 8
Positiv to Pedal 8-4
3 manuals, 41 ranks