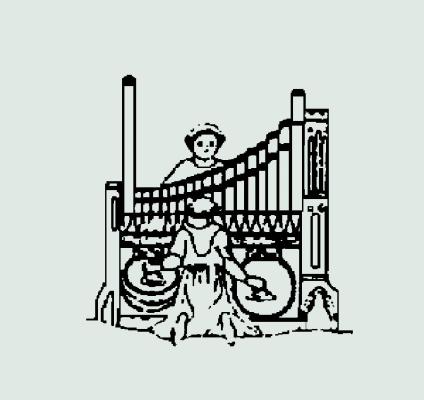
Emery Brothers, Allentown, Pennsylvania
St. Stephen’s Episcopal Church, Richmond, Virginia
Founded in 1911, St. Stephen’s Episcopal Church is not old by Virginia standards. Located in the Westhampton section of the city near the then recently relocated University of Richmond, the new Country Club of Virginia, and two diocesan schools, St. Christopher’s for boys and St. Catherine’s for girls, the church was begun by several families who wanted a more convenient location for their children to attend Sunday School. For this reason the church was known early on by the playful moniker St. Convenience, an appellation that in certain circles persists to this day.
The new church flourished as did the neighborhood. Just before the stock market crash and Great Depression, a new church in the Gothic Revival style was built at the end of Grove Avenue. In the archives of the church there exists an elaborate elevation drawing showing the proposed new church in the Georgian style, which is ubiquitous throughout Richmond. I have never learned who prevailed on the new church to adopt Gothic, but it was probably inspired by the new buildings of the University of Richmond, which were designed by Ralph Adams Cram. The vestry approached Cram about designing their new church. By this time Cram, whose wife was from Virginia, had completed the original buildings of the University of Richmond in its new Westhampton campus, as well as several other projects in Richmond and other locations in Virginia. But Cram replied he was too busy to accept the commission, and he recommended Frank Watson of Philadelphia. Watson designed the church with a seating capacity of about 400. A new organ built by Hook & Hastings was installed in the new church.
In the years following World War II, the parish experienced exponential growth, to the point where the church was considerably enlarged to a design by Philip Hubert Frohman, the architect of Washington National Cathedral. Frohman’s design increased the seating capacity to approximately 750 by extending the original north aisle to become a chapel, extending the nave two bays westward, and creating an imposing three-portal entrance. For this enlarged church the Aeolian-Skinner Organ Company built its Opus 1110, designed and tonally finished by G. Donald Harrison, and installed in 1951. Emerson Richards was a consultant to the church, and it was he who was responsible for building the shelf into the chancel to contain the Great and Pedal divisions outside the chamber arch. The previous organ was completely contained in the chamber and the façade of non-speaking pipes was flush with the chancel wall.
There was protracted correspondence between the church and Harrison about the new façade, which required a few non-speaking pipes to form a link between the two original portions of the old façades, so that it would appear as one continuous panel. Aeolian-Skinner typically did not do this type of work, as all casework was considered above and beyond the contract for a new organ. But representatives of the church were adamant, and Harrison relented and made the few required dummy pipes and woodwork to link the two. Also, by this time post-World War II inflation caused Aeolian-Skinner, who typically took three years to build an organ, to include escalator clauses into their contracts, which could increase the contract price to a ceiling amount should costs increase significantly during the period it took to build the organ. Many potential buyers of their organs balked at this, but those who truly wanted an Aeolian-Skinner organ accepted it. That Harrison reluctantly agreed to waive this clause in the case of St. Stephen’s Church indicates to me that the businessmen representing the church were iron-fisted in their resolve that the church pay no more than it absolutely had to, and is also evidence that Harrison really wanted to build the organ!
During these negotiations the church ordered a Dun & Bradstreet report on Aeolian-Skinner, and the results are sobering in retrospect and portend bad times to come. Even though Aeolian-Skinner was very busy at the time building some of its most famous organs, the various vicissitudes that eventually caused the demise of the company some two decades later were beginning to evidence themselves. The provider of the report commented, “The firm in Hagers-town had a rating in Dun & Bradstreet of A-1 so we did not get a report on them. Between the two companies based on the rating in Dun & Bradstreet I would prefer buying it from the Hagerstown company other things being equal.”
The organ was rather modest for the large new space. It consisted of three manuals and forty-one ranks. The sound, while beautiful and conforming to all the hallmarks of Harrison’s American Classic organ, filled the church in a similarly modest way. In 1968 Aeolian-Skinner made significant additions to the organ: a new Positiv division on the Epistle side of the chancel, an Antiphonal Organ at the west end of the church surrounding a new stained glass window, several ranks in the main organ, including a 32′ reed and a second mixture in the Great, and a new four-manual console. The original three-manual console was sold to Trinity Church in Rutland, Vermont, where it still exists today. These additions were designed by Joseph S. Whiteford, who was by this time retired from the company. But he was friends with the organist of the church, Granville Munson (my predecessor), and had been a classmate of his at St. Alban’s School in Washington. So Whiteford left his retirement to work on the job, even donating a new stop in honor of his friendship. The only alteration to Harrison’s original organ was the reworking of the Swell Flute Celeste, making it an 8′ stop; it had previously been a 4′ stop.
This was the organ that I inherited when I became organist of the church in 1985. At about this time the long-time tuner of the organ retired and there were a few deferred maintenance items that needed attention. There were also tuning irregularities inherent with the various spatial placements over a large area, and the unusual effects of the air conditioning system. Through mutual associations I learned of Stephen Emery, who was at that time installing an organ in nearby Williamsburg for Petty-Madden Organbuilders, for whom he then worked. It was soon arranged for Steve to come by the church, and the short story is that he, and later his brothers and co-workers, have lovingly maintained the organ ever since. In short order Steve took care of the mechanical repairs that were needed, but most important, he quickly found the best way to keep the various divisions in absolute tune. There may be others as good, but there is no one who surpasses Steve as a tuner, as he just has the knack to understand difficult spatial arrangements and inherent temperature fluctuations. He also coached us in the proper use of the air conditioning system, especially the length of time necessary to maintain a precise temperature for tuning sessions, services, and concerts. The system, built in the 1960s, was the finest available at the time, and the church wisely maintained a near-constant temperature throughout the seasons, to the point where, summer or winter, the temperature in the organ fluctuated only slightly. The church also benefited greatly from the fact that Steve and his coworkers traveled regularly to their various jobs in the South. I cannot recall a significant concert, recital, or recording session when they weren’t right there working alongside us all for a good outcome. They were truly part of our team in the music ministry of the church.
In my early years at the church we soon recognized the desirability of making some modest changes in the chancel area to reflect the wide range of uses required of the church in its various pageants, concerts, and the then-yearly organ recital series. The two diocesan schools also regularly held services and events in the church that would be helped by a certain flexibility of space within the small chancel. All the while it was understood that the basic classic “feel” of the divided chancel not be compromised. The church invited Terry Byrd Eason to visit the church, and over a year of conversations and meetings with various stakeholders he developed a scheme which, although it took almost 30 years, is the basic plan that was implemented in 2016. This plan called for new marble flooring, flexible seating, extending the chancel floor slightly westward into the nave, and a movable organ console.
As the original organ approached its 50th anniversary it began to show the telltale signs of aging leather. The vestry, knowing the eventual need, opted to undertake a complete restoration of the organ before it became critical. This work consisted of taking the organ down one section at a time to replace the leather components and clean all the pipework. Some of the original stops were cone tuned, which resulted in some minor damage to the pipework, mainly in the upperwork and mixtures. These pipes were repaired and outfitted with new tuning slides. All pipework (except the lowest basses) was removed to Emery Brothers’ shop for cleaning and repair as needed. This work was undertaken from 2002–2004. During this time, while various divisions were out, other portions of the organ were available to cover services, and at no time was the liturgical schedule compromised or did the church require a substitute organ to be brought in. The newly restored organ was celebrated in March 2004 in a weekend of recitals, services, lectures, and tours featuring Judith and Gerre Hancock, Charles Callahan, and Steve Emery, who gave tours of the organ at various times throughout the weekend and on Sunday between and after services. At this time Walker Technical Company provided a new solid-state combination action. The old pneumatic combination action was disconnected, but left in place.
The one item of organ restoration that was not undertaken during 2002–2004 was the console, which retained its pneumatic mechanism and wax-coated wiring from 1968. Some of the less-invasive parts of Terry Eason’s design were quietly implemented in the ensuing years, including work to make the main altar freestanding. However, the work on the console was tied to the redesign of the chancel and was undertaken after I left the church in 2006. I was not involved in this work, which was folded into a massive, complete nine-million-dollar renovation to the entire church in 2014–2016. It included replacing the entire floor of the church and chancel, making the entrances fully accessible, the redesign of the chancel, replacement of the HVAC systems, and outfitting the console with new controls and making it movable. During the 18-month renovation, it was necessary to remove the entire organ due to the invasive nature of the work and the amount of dust created, as the entire interior of the church space was a major construction site. Services were held in the Parish Hall and Palmer Hall Chapel during this time.
Along with a full church I heard the spectacular results for myself at a concert and Evensong for the American Guild of Organists Regional Convention in June 2017 sung by the Choir of the Church of the Epiphany, Washington, D.C., directed by Jeremy Filsell, with Erik Wm. Suter, organist. Visually and tonally, the project is a thing of great beauty and was inspiring to experience.
—Neal Campbell
Trinity Church, Vero Beach, Florida
Aeolian-Skinner Opus 1110 is truly a beautiful instrument, especially in its recently improved acoustic environment. In short this is a pipe organ most everyone will find easy to love. It has been our pleasure to maintain this instrument for over 30 years. The project we undertook in the early 2000s included total mechanical renovation of the organ, releathering windchests and reservoirs, tremolos, shade engines, and pipework cleaning and restoration. In 2014 we removed exposed pipework, covered winchests, covered enclosed divisions, and removed the console in preparation for a major construction project in the church.
This also presented the perfect opportunity for a thorough console rebuild. The whole organ was rewired to a new Solid State Organ Sytems Multisystem, and the console fitted out with multi-level memory, piston sequencer, and SSOS’s newly unveiled Organist Palette. We also added internal casters to the console and pedalboard to make the console movable.
We are deeply grateful to the people of St. Stephen’s for their ongoing commitment to Aeolian-Skinner Opus 1110 and for the opportunity to partner with them in preserving and presenting this fine instrument.
—Adam Dieffenbach
Owner, Emery Brothers
Builder’s website:
Church website: www.ststephensrva.org
GREAT
16′ Quintaton 61
8′ Principal 61
8′ Spitzflöte 61
8′ Bourdon 61
4′ Principal 61
4′ Rohrflöte 61
22⁄3′ Twelfth 61
2′ Fifteenth 61
IV Fourniture 244
II–III Cymbale 157
8′ Trompette de Fête 61
4′ Clairon de Fête (ext 8′) 12
SWELL (enclosed)
8′ Geigen Principal 68
8′ Stopped Diapason 68
8′ Viole de Gambe 68
8′ Viole Celeste 68
8′ Flute Celeste II 124
4′ Principal 68
4′ Flauto Traverso 68
2′ Octavin 61
IV Plein Jeu 244
16′ Contre Hautbois (ext 8′) 12
8′ Trompette 68
8′ Hautbois 68
4′ Clairon 68
Tremulant
CHOIR (enclosed)
8′ Viola 68
8′ Viola Celeste 68
8′ Singendgedeckt 68
8′ Erzähler 68
8′ Kleine Erzähler 68
22⁄3′ Nazard 61
2′ Blockflöte 61
13⁄5′ Tierce 61
8′ Clarinet 68
Tremulant
POSITIV
8′ Holzgedeckt 61
4′ Prinzipal 61
4′ Spillflöte 61
2′ Lieblichprinzipal 61
11⁄3′ Larigot 61
1′ Sifflöte 61
III Scharf 183
ANTIPHONAL
8′ Prinzipal 61
4′ Præstant 61
2′ Flachflöte 61
IV–VI Mixture 289
8′ Trompette de Fête (Gt)
4′ Clairon de Fête (Gt)
ANTIPHONAL PEDAL
16′ Sub Prinzipal (ext Ant 8′) 12
PEDAL
32′ Resultant
16′ Principal Bass 32
16′ Bourdon 32
16′ Echo Lieblich (ext Sw 8′ St Diap) 12
16′ Quintaton (Gt)
8′ Principal 32
8′ Flute (ext 16′ Bourdon) 12
4′ Super Octave (ext 8′ Prin) 12
4′ Spitzflöte 32
IV Fourniture 128
32′ Contre Bombarde (ext 16′) 12
16′ Bombarde 32
16′ Contre Haubois (Sw)
8′ Trompette (ext 16′) 12
4′ Clairon (ext 16′) 12
63 stops
69 ranks
3,999 pipes