Pianist and harmoniumist Artis Wodehouse has a BM from the Manhattan School of Music, an MM from Yale, and a DMA from Stanford. A National Endowment for the Humanities grant led to her producing CDs and publishing transcriptions of recorded performances and piano rolls made by George Gershwin, Jelly Roll Morton, and Zez Confrey. In 2000, Wodehouse began performing on antique reed organs and harmoniums that she had painstakingly restored and brought to concert condition. She founded the chamber group MELODEON in 2010 to present little-known but valuable music from 19th- and early 20th-century America, using her antique instrument collection as the basis for repertoire choice.
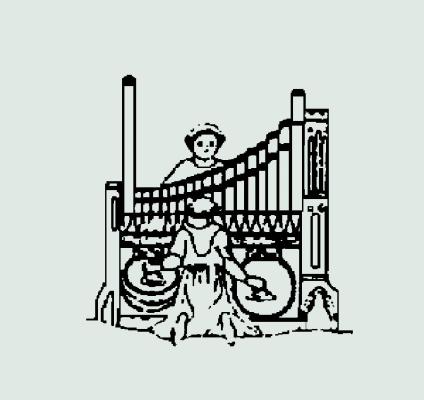
During its prime in the nineteenth-century, the reed organ was the preferred instrument in American homes and also deemed a fit substitute for the more expensive pipe organ. Large reed organs became common in civic gathering halls and smaller churches. Despite the popularity of reed organs in America,1 music for them consisted primarily of simplified arrangements of European art music, easy-to-play popular and sentimental ditties, polkas, marches, and waltzes, or hymns and other service music associated with worship or civic gatherings.
Toward the end of the nineteenth century it became apparent that design variation from company to company and from organ to organ, even within a given company’s fleet of models, was preventing composers from writing idiomatic original music for the American reed organ. The limited market for music crafted for one or another of the competing designs was too small to sustain widespread printing and marketing of scores.2
Without its own literature, such as had been created during the nineteenth century for its European counterpart, the harmonium, the American reed organ had an uncertain future. It would continue to be regarded at best as “a sort of weak substitute for the church organ.”3 Then, in the mid-1890s, at essentially the beginning of the end of the reed organ era, Mason & Hamlin4 began to address the problem by introducing an action design5 whose capabilities would “insure the greatest advantages to the composers, at the same time enable the manufacturer to place his instruments on the market at as low a price as possible.” The new action design was called the “Normal-Harmonium.” This was the action design for which the American composer Arthur Bird (1856–1923) wrote his compelling body of reed organ music. Figure 1 shows the Mason & Hamlin American reed organ, with Normal-Harmonium action design. Two knee levers are above the foot pedals. The right lever controls the internal swell shades; the left lever activates the Grand Jeu.
Mason & Hamlin’s Normal-Harmonium action design and Arthur Bird’s creation of a substantial, idiomatic music for the American reed organ came too late. Piano sales that had roared ahead after the Civil War rapidly displaced the reed organ. In the 1880s, reed organ sales slipped below that of pianos. By World War I, the glory days of the reed organ were over.6
Two competing
19th-century instruments:
The American reed organ
and the European harmonium
In the 1840s, United States inventors and businessmen founded companies that offered distinctive fleets of reed organ models. Reed organs were built in a bewildering variety of brands, sizes, and stoplist configurations. They ranged from diminutive four-octave home models that traveled to the West in covered wagons, to large, expensive instruments with powerful tone, full pedalboards, and many stops.
The American reed organ used one or more sets of brass “free reeds” in order to generate tone. The performer’s foot pumping activated suction bellows that generated a stream of moving air, much like a vacuum cleaner. When the performer depressed a key, this moving air passed through a small chamber in which the reed was affixed at one end, but free to vibrate on the other end (hence the designation, “free reed”). The reeds varied in length, and the longer the reed, the lower the tone. Air rushing through the chamber caused the reed to vibrate, and tone to be produced. When a reed organ had more than one set of reeds, a set could be brought into play or silenced by allowing or blocking the moving air via stop pulls. As with the pipe organ, a set of shutters or swell shades located within the action facilitated dynamic contrasts. The performer opened or shut them on a gradient via a knee paddle.
The largest and most prominent reed organ companies were Mason & Hamlin in Boston and Estey in Brattleboro, Vermont, but scores of others proved successful. As the nineteenth century progressed, American reed organs became increasingly complex. Inventors developed voicing techniques that produced a broad range of distinctive and contrasting timbres, named using terms derived from pipe organ nomenclature.7 Instruments built with multiple sets of differently voiced reeds featured multiple stops and a divided keyboard8 so that the player could choose contrasting timbres in the treble and bass of a single keyboard. Large reed organs were sometimes built with multiple keyboards, like pipe organs. The more reeds in an instrument, the more expensive it would be.
Another keyboard instrument employing differently voiced sets of free reeds in airtight chambers arose in Europe during the nineteenth century. A Frenchman, Alexandre Debain, patented this instrument in 1842, naming it a “harmonium.” (See Figure 2.)
Like the American reed organ, the European harmonium came to offer a broad range of distinctive and contrasting timbres controlled by stop pulls, and a divided keyboard that enabled the choice of different timbres in the treble and bass. (See Figure 3.)
Despite some similarity in design to the American reed organ, the European harmonium did not employ the American-style bellows system (suction) that pulled moving air in and through the reed chamber. Instead, in the European system, air was pushed through and out via pressure, producing sound like a trumpet or an oboe. The different airflow systems require different technical skills of the performer and produce distinctly different tonal characteristics. (See Figure 4.)
Foot pumping on the harmonium manages two important functions because of the way harmonium bellows were designed to work: the performer maintains constant airflow while simultaneously adjusting the relative airflow speed responsible for dynamic contrasts.9 Manipulating airflow velocity to effect dynamic changes was called “expression,” and this function had its own specially assigned stop pull. An additional European innovation for facilitating dynamic contrast was the invention of the so-called “double expression.” It was installed in the more costly European harmoniums. Double expression, a capability arising no doubt from a desire to mimic the piano’s ability to balance melody and accompaniment, allowed the performer to control not only the overall loudness but also the relative volume of the treble and bass on a gradient. Double expression is controlled by two knee levers installed under the keyboard and above the two foot-pump pedals. The skill required to play smoothly and expressively on the harmonium demands much practice.
Late-speaking reeds, i.e., those with a time lag between the act of depressing a key and the sounding of its corresponding tone, hampered performers on both the American reed organ and the European harmonium.10 Although quick airflow delivery to the reeds was a design priority for both reed organ and harmonium builders, the Americans felt that beyond a certain point, slight lags were an acceptable characteristic of the instrument for which the performer was expected to make appropriate adjustments. The Europeans, however, took a different approach. To mitigate the problem of late speech (and to provide an additional tonal effect) they positioned small felt-covered hammers next to each of the reeds of the set most frequently used in performance. These little hammers were controlled by a stop pull, referred to as “percussion.” When the percussion stop is pulled and a key is depressed, the little hammers simultaneously strike the sounding reed, causing it to speak more quickly and incisively, like a crisp piano attack. The harmonium’s percussion makes performance of rapid passagework more predictable when compared to the American reed organ.
The most far-reaching advantage the harmonium held over the American reed organ was the standardization of stops generally agreed upon by the European companies. Standardization had two benefits: it made it possible to print in music scores commonly understood registration that could be used across instruments built by different companies. Secondly, performers could move from one harmonium to another with a minimum of adjustment.11
It should be noted that the terms “harmonium” and “reed organ” were and continue to be used interchangeably. Lack of a clear and consistent terminology must be laid at the door of the overlapping and competing terms originally used. In their heyday, American reed organs were most frequently referred to as simply “organs,” but other names were used as well. These included Organ-Harmonium and Cabinet Organ, two different terms used by the same company, Mason & Hamlin. There were also fanciful names such as Phonorium, used by Estey.12
Harmonium and American reed organ repertoire
The capabilities of the European harmonium and the move towards standardization13 attracted several important nineteenth-century European composers. Elgar, Strauss, Schoenberg, Webern, Mahler, Liszt, Tchaikovsky, and Rossini made good use of the harmonium in some of their orchestral and/or choral works. Berlioz, Franck, Saint-Saëns, Guilmant, Widor, and many others wrote high quality solo and chamber music for it. Finally, the German composer Sigfrid Karg-Elert (1877–1933) made it his mission to develop a body of repertoire that would exploit the unique sonic and expressive capabilities of the Art Harmonium. During the early twentieth century Karg-Elert wrote what has proved to be the single most significant body of solo and chamber music for the instrument. The popularity of the European harmonium peaked about 1900, slightly later than the American reed organ’s peak of popularity.
Relatively few harmoniums made it across the Atlantic during the nineteenth century. On the other hand, American reed organs were exported and sold in fair numbers throughout Europe, particularly those built by Mason & Hamlin.14 Also, several European manufacturers such as Lindholm, Mannborg, and Shiedmayer adopted the American suction bellows system for their instruments.15 Nevertheless, despite significant cross-Atlantic distribution of the American reed organ and the availability of native European instruments with some shared characteristics, the American reed organ never established an artistic foothold through a representative body of high-quality music comparable to that written for the harmonium. This cannot be fully explained by the technical differences between the two as outlined above. Although the American instrument may have lacked the harmonium’s more refined control of dynamics and its useful percussion stop, the best American instruments, such as the Mason & Hamlin Liszt Organ, have a distinctive tonal beauty and a multiplicity of sounds equal to those of their European counterparts.
The promotional prominence and enlarged, relatively standardized capabilities of Mason & Hamlin’s flagship Liszt Organ may therefore have been the impetus behind Boston-based American publisher Arthur Schmidt to print a few works for it during the 1890s. Schmidt’s publications for the Liszt Organ included both original compositions as well as arrangements of famous European works for organ solo, duets with piano, and chamber pieces. But apart from Eugene Gigout’s excellent Romanza for the Liszt Organ, unfortunately none of the rest rose to a similarly high quality.
Arthur Bird, American expatriate composer (1856–1923)
Around 1896, Mason & Hamlin likely encouraged and may have actually commissioned the American composer Arthur Bird to write idiomatic art music for the standardized action they introduced during the 1890s, called the Normal-Harmonium.
No documentation has yet surfaced indicating payment to Bird for his work by the firm. Nevertheless, key musical and personal circumstances link Arthur Bird to the most significant people associated with the Mason & Hamlin Company. Central to the connection between Arthur Bird and Mason & Hamlin was Franz Liszt. A canny seer, Liszt bet correctly on the ability of eager young American pianists and composers to hold high the torch of pianism and to carry forward the music of the future. Liszt welcomed them, offering his inspired pedagogy and worldly professional connections free of charge. Liszt’s generosity forged a well-documented bond among his pupils. Liszt’s first American student was the pianist William Mason (1829–1908). Mason studied with Liszt beginning in 1849, and brought back to the United States Liszt’s pedagogic principles through an extensive career of teaching, performing, and publishing. William Mason also happened to be the brother of Henry Mason, who in 1854 co-founded the Mason & Hamlin Company. Henry and William Mason were in turn sons of Lowell Mason, an important American hymn composer and musical educator during the first half of the nineteenth century.
Liszt owned and wrote music for numerous keyboard instruments provided for him by both European and American companies.16 Among such instruments in his sizable collection was a Mason & Hamlin cabinet organ that he acquired in the 1870s. Later, Mason & Hamlin’s flagship high-end model came to be named the “Liszt Organ,” a likely outcome of the close connection between Liszt, his pupil William Mason, and the Mason & Hamlin Company.17 The Mason & Hamlin Liszt Organ was introduced about 1880. Complex, colorful, powerful, and versatile, the Liszt Organ was designed to compete with the best European harmoniums. While the Liszt Organ shared many tonal and functional features with the Normal-Harmonium design, it had a different tessitura (five octaves, C to C, versus the Normal-Harmonium’s F to F) and a different split point (E–F versus B–C for the Normal-Harmonium).
Arthur Bird was also one of Liszt’s American pupils, coming to him during Liszt’s later years.18 Bird’s musical and personal background strikingly resembled that of William Mason. Born in Belmont, Massachusetts in 1856, Bird’s early musical training came from his father and uncle, who were born-and-bred American church musicians. Arthur’s father, Horace Bird, and his uncle, Joseph Bird, were active in the New England of the 1840s and 1850s as voice teachers, composers of hymns and songs, and editors of singing books written to develop score-reading literacy. Upon the advice of William Mason’s father, Lowell Mason, young Arthur Bird was sent in 1875 to study in Germany at the Berlin Hochschule für Musik. Returning to North America two years later, he took a church music position in Halifax, Nova Scotia, where he began to compose. He returned to Berlin in 1881 to study composition and orchestration. It was during this time that Bird came into the Liszt orbit.
By his early 30s (in the mid-1880s), Bird had become well established as an organist and pianist. His compositions were published and performed widely in Europe. Bird spent most of his life abroad, mainly in Berlin, where he married a wealthy German widow and apparently lived lavishly. In 1897 Bird returned for some time to the United States in what proved to be a failed attempt to have his comic operetta, Daphne, performed in America. Reading between the lines of William Loring’s biographical work on Arthur Bird, is it possible that Bird wished to forge a closer connection to his native country? Certainly a major production of an opera by a United States-born composer within the United States would be an excellent vehicle for that scenario. During the late 1890s, when the quest for “genuine” American composers was in full swing, Bird may have sensed an opportunity. In any event, in that same year (1897), the first of Bird’s pieces for the Mason & Hamlin “American Harmonium” (op. 37) were published by Breitkopf and Härtel, an important German firm still operating that publishes high-art European music.19
Characteristics of Arthur Bird’s “American Harmonium”
The historic trajectory mating Arthur Bird with the Normal-Harmonium came just at the point when the piano had overtaken reed organ sales. Mason & Hamlin realized that in order to survive in the long term, the reed organ needed some good original music. The publication of Arthur Bird’s music for the “American Harmonium” came at a historic crossroad for the American reed organ, largely due to the rise of the American piano. From the 1850s, pianos, and particularly American pianos, started to benefit from standardization and mechanical manufacturing methods of the industrial revolution. Prior to this time, pianos were mainly handcrafted items. Likewise around 1850, the design of the piano, particularly the American piano, moved rapidly toward increased durability and a greater dynamic and pitch range. Piano types coalesced into three categories: square, grand, and finally, upright. Each of these types served a clear purpose. As a result, consumers began to turn to the piano as a viable keyboard alternative to the reed organ, particularly in the home market, where the reed organ had ruled uncontested.20 Sales of pianos grew steadily through the nineteenth century.
In contrast to the piano industry, American reed organ manufacturers from the 1850s to the 1900s offered consumers instruments of a wide variety of sizes, competing capabilities, nomenclature, and above all, case styles.21 After the Civil War, American manufacturers also developed complex instruments of considerable beauty, sophistication, and expense. These large instruments with enhanced performance capabilities were aimed at a smaller “niche” market, for placement in the homes of the wealthy, civic or religious meeting halls, and small churches. But after a sustained growth period lasting about 40 years, sales of the American reed organ began to decline in the 1880s.
The Normal-Harmonium action design of the 1890s for which Bird wrote was conceived to meet these market challenges. Mason & Hamlin worked with and adopted the Normal-Harmonium design in collaboration with two entities associated with the company: their German representative Paul Koeppen and the Bender firm in Leiden, Holland.22 Mason & Hamlin’s goal was to provide a standardized instrument that could compete with the piano and its plentiful repertoire. Their instrument had to be sophisticated enough to attract composers to write good music for it and be of a reasonable cost.
Mason & Hamlin met both of its goals. First, the cost of an instrument with Normal-Harmonium specifications was indeed lower by half or more than that of the top of the Mason & Hamlin line, the Liszt Organ. The price of the Liszt came in at $700, but instruments with Normal-Harmonium capabilities could be had between $260 and $300.23 Second, the Normal-Harmonium action provided attractive and useful performance capabilities. These included a pitch range of five octaves from F to F and multiple sets of reeds offering an elaborate stoplist. American reed organs with the Normal-Harmonium action design began to be manufactured in the 1890s and continued to be built until the company ceased reed organ production in the early 1920s.
As mentioned previously, inconsistent nomenclature and lack of a simple explanation for actual performance capability plagued the field. Although Mason & Hamlin offered a standardized action design in the Normal-Harmonium, Bird’s music itself was identified on the score as being intended for the “American Harmonium” and/or the “Normal-Harmonium.” Nomenclature had still not jelled. Therefore it must be stressed that the terms “American Harmonium” and Mason & Hamlin “Normal-Harmonium” do not refer to any one specific instrument, but rather to an action design embodying certain specific capabilities.
Figure 5 shows the overhead view of interior of the Mason & Hamlin American organ with Normal-Harmonium specs. To the upper right is the paddle that is activated to rotate by the Vox Humana stop. The upper left box houses the very large Sub Bass reeds. The specific capabilities of the Normal-Harmonium are as follows.
Stoplist:
Diapason Dolce 8′—the Diapason, mechanically softened.
Sub Bass 16′—consists of 13 notes, the chromatic octave upward from low C. This stop uses the largest, longest reeds, producing a deep, rich, and powerful sound.
Eolian Harp 2′—two detuned sets of reeds producing a shimmering, ethereal vibrato.
Diapason 8′—pure, organ-like tone.
Viola 4′—resembles the sound of the orchestral instrument for which it is named.
Viola Dolce 4′—the Viola, mechanically softened.
Vox Humana—adds a vibrato or tremolo. Can be used in combination with any of the other drawn stops in the treble. Activated by the turning of a windmill-like paddle located inside the action.
Seraphone 8′—differs from the Diapason in timbre. Focused and slightly nasal.
Flute 4′—resembles the sound of the orchestral instrument for which it is named.
Melodia 8′—continuation in the treble of the Diapason reeds.
Vox Celeste 8′—another stop combining two sets of detuned reeds that creates a vibrato effect.
Octave Coupler—when pulled, mechanically connects a note to that of one an octave higher.
Melodia Dolce 8′—mechanically softened Melodia.
The split point on the keyboard is between B and middle C. Stops from Seraphone 8′ up activate the treble, the stops from Viola Dolce, down, the bass.
Mechanical devices:
Grand Jeu—activated by a knee paddle located under the keys above the left foot pump pedal. The Grand Jeu causes all the reeds to sound at once, producing the instrument’s fullest and loudest sound.
Swell—activated by a knee paddle located under the keys above the right foot pump pedal. This device controls the internal shutters responsible for dynamic contrasts. (See Figure 6.)
Arthur Bird as composer
During his lifetime, Arthur Bird was recognized as an active, widely published, and well-received composer of some stature, particularly in Europe. Incidentally, his successful European career was launched in no small part because of the positive public and private endorsements Bird received from the influential Franz Liszt.
Bird’s oeuvre is extensive, including opera and theatre works, orchestral music, songs, piano materials, chamber works (particularly those for wind instruments, for which he is best-remembered today), organ, and many other forms. Bird wrote a sizeable number of short solo piano pieces in well-established standard dance forms and topical styles—march, waltz, minuet, gavotte, lullaby, and mazurka. His extensive experience composing in this genre prepared Bird well to write for the American reed organ. Bird’s music is available in score at the Library of Congress through the generous donation of his widow and has been amply documented through the International Music Score Library Project.24
Relatively little of Bird’s music has been recorded.25 What is available tends to confirm the critical reception his work received during his lifetime. Reviewing a performance of [Bird’s] Serenade for Wind Instruments, op. 40, the Berliner Borsen Courier said: “It is distinguished for the freshness and spontaneity of its invention, as well as the clever craftsmanship and the clear and compact disposition of its different parts . . .” Another critic comments: “Characteristically his music is pleasing and melodious in composition. It is coherent and well developed in form. It lies easily within the range of the instruments, and displays no little knowledge of their resources.” Of him, [Arthur] Farwell wrote: “Arthur Bird is known as the possessor of a fertile and truly musical imagination and a thorough technique . . .
Bird is a musician of German training and French sympathies and calls himself a conditional modernist.” Mentioning that Bird composed in almost all forms, [Louis] Elson says of him: “He is an excellent contrapuntist, yet uses his skill in this direction as a means rather than as an end, seldom making a display of his knowledge. It is a pleasure to find an American composer who is not anxious to out-Wagner and who goes along the peaceful tenor of recognized and classical ways.”26 Bird was even described as “the most promising American composer of the middle and late Eighties” by no less than the important conductor,
Arthur Nikisch.27
The amount and dating of Bird’s production seem to confirm Loring’s supposition28 that after 1900, Bird’s work dwindled, though his reed organ works of 1905 (op. 45) maintain his previously held high standard. On the other hand, his simplified arrangements, American Melodies Specially Adapted and Arranged for Normal-Harmonium of 1907, appear to have been written simply for profit and lack the artistic value of his earlier work for the American Harmonium.
Arthur Bird’s music for the American Harmonium
Those who either possessed or might have considered purchasing an instrument with the Normal-Harmonium action design would likely be individuals of some performance ability and/or a level of musical sophistication high enough to appreciate the artistic features of the instrument. They would also likely appreciate piano music of the better salon variety, up to and including Schumann’s, Chopin’s, or Grieg’s short works for solo piano. Finally, they would most likely be of the social class that would appreciate hearing this music, most likely in the home setting.
Bird’s conservatism—informed by fine craftsmanship, deft handling of instrumental color, and fluency in miniature forms—may not have been enough to place him into the compositional pantheon of his trailblazing European contemporaries (Mahler, Debussy, etc.), but his abilities ideally suited him for writing salon-oriented character pieces of the type popularized by Mason & Hamlin’s Normal-Harmonium. An already accomplished American composer, Bird’s impeccable, media-worthy credentials and network of connections to Mason & Hamlin were a further plus. Bird was a perfect fit.
Bird published six opus numbers for the Normal-Harmonium.29 All contain interesting and beautiful music, but the best of these was his first, the ten pieces of op. 37.30 In the first printing, the op. 37 pieces were identified directly on the score’s front pages as being intended for the “American Harmonium”31 or for the Mason & Hamlin “Normal-Harmonium.” A page is devoted to an explanation of the stops required and their manner of notation in the score. Bird used circled letters derived from the stop name. For instance, Diapason is D; Viola, V; Voix Celeste, VC; and so forth. Later print runs of op. 37 contain the same explanatory page, but also indicate standard stop numbers, i.e., 1 for Diapason, 3 for Viola, 5 for Eolian Harp, etc., that would correspond to numbers appearing on European suction instruments of equivalent capability.32
While no piece in the op. 37 set lasts more than three minutes, each exhibits a mastery of craft: beautifully spun-out melodies, masterful counterpoint, subtly personalized inflections of nineteenth-century harmonic practice, and traditional formal structures handled with deft assurance. Bird’s forms are not unusual (ABA, sonata, rondo). But because the Normal-Harmonium’s unique instrumental colors are an integral component of Bird’s structural designs, the listener experiences an additional dimension of thematic transformation. In his music for Normal-Harmonium, Bird’s assimilation of instrumental color as a component of structural rhetoric relates his music to that of the nascent French impressionists at the turn-of-the-century. The following briefly describes salient features of each of the pieces in Bird’s op. 37:
1. Meditation—a sarabande. In this mini-Wagnerian contrapuntal ramble, Bird employs kaleidoscopic stop changes that underscore the evolving melodic twists and turns.
2. Preludium—brooding and dramatic four-part writing in an ABA structure. Registration is simple, but Bird uses the octave coupler at the recapitulation, reinforcing and underscoring the harmonic excursions introduced as the piece moves toward an impassioned final cadence.
3. Adagio—elegiac four-part mini-sonata. Development section comprises a series of recitative-like meandering arpeggios over sustained chords. Recapitulation re-registers the opening material over low pedal points. With more recitative-like arpeggios at the coda, the piece concludes with a simple fadeout on the ethereal Eolian Harp stop.
4. Reverie—features a long-breathed, haunting, and tentative treble melody on the flute stop set against slithering countermelodies registered on the atmospheric Eolian Harp stop. In ABA form, the melody’s return is entirely recast in a fuller texture with the foundation 8′ and 4′ stops. In partnership with a walking bass line, the melody’s tentative first appearance is thereby transformed into an affirmative point of arrival. The coda brings the listener back to the ethereal Eeolian Harp, rounding the piece off as it began.33
5. Postlude—hearkens back to Bird’s American past, a spirited march that suggests a full wind band.34 Bird’s registration indicates that the piece must be played in its entirety using only one setting, the circled G indicating “Grand Jeu.” Because Grand Jeu causes all the stops to sound at once, finger strength and vigorous foot pumping are required throughout.
6. Improvisato—a fierce, somewhat virtuosic piece. Registration involving the basic 8′ and 4′ stops is augmented at the recapitulation by use of the Grand Jeu. Rapid, conjunct passagework in the wild coda comes off surprisingly well, despite the lack of a percussion stop. Bird was a hands-on composer and knew what the Mason & Hamlin organ could do.35
7. Offertoire—This piece would be suitable for use in a church setting. It is an atmospheric sweet/sour composition with change of mode.
8. Scherzo—This is the most technically demanding of the set, an extended rondo. Rapid sixteenth notes scattered throughout the piece when the octave-coupler is drawn or the Grand Jeu is activated require finger strength and precise articulation. Not only the performer’s skill is tested: Bird takes the instrument itself to the edge of its mechanical ability to sound quick notes on the fly. Registration is extraordinarily full and rich, suggesting an orchestra.
9. Auf dem Lande—a melancholy, minor “folksong” melody is transformed to a grand, affirmative conclusion in major mode.
10. Pastoral—perhaps the most inventive and idiomatic of the entire set. Bird’s motivic ideas have a symbiotic relationship with the instrumental colors he brings to bear. Set above continuously sustained low pedal points, a flowing conjunct melody in the treble twines about an ostinato pattern in the mid range. In order to keep the pedal points depressed while so much action is occurring that requires two hands, lead weights must be used to hold down the pedal-point notes.
The American reed organ, Arthur Bird, and the future
The composition of high-quality, original repertoire for the European harmonium during the nineteenth century has proved to have far-reaching consequences. Once thought lost to history, beginning in the 1980s the harmonium has been going through a steady revival, centering in the Netherlands. It seems likely the harmonium will continue to reestablish the place it once held in the classical repertoire. While there continues to be a small but passionate interest in the American reed organ,36 a revival similar in scope and momentum has not yet begun.
As the rise and fall of the American reed organ demonstrates, the key to an instrument’s survival is not its mechanical capabilities, but rather the repertoire written for it. Not just any music will do. What is needed is music that will continue to offer listeners an aesthetic experience independent from the era in which it was created.
In the case of the European harmonium, the point where form and function met occurred when distribution was growing and the instrument’s capability achieved sufficient standardization. This favorable environment attracted a fair number of composers to write significant music for it. Unfortunately for the American reed organ, standardization arrived at the very point when distribution was falling.
Nevertheless, we are grateful that one composer, Arthur Bird, stepped in during a brief moment of opportunity in the history of the American reed organ. With his ideal combination of skills, commitment, and inspiration, he provided us with music that stands poised to move into the future. ν
Special thanks to Carson Cooman and Whitney Slaten
Notes
1. American publishers also churned out a deluge of reed organ method books intended for the large market of rank amateurs in the United States.
2. Paul Hassenstein, “The Normal Harmonium And Its Literature,” The Music Trade Review 41:3, July 1905, 87.
3. Ibid., 87.
4. Mason & Hamlin began as a reed organ manufacturer, but in 1883 started making pianos as well. About 1920 the company ceased making reed organs, but continued their piano line.
5. “Action design” refers to a specific set of performance capabilities contained within the mechanism of an instrument. Action design was independent of case style. The same action could be enclosed in a variety of cases.
6. Robert F. Gellerman, The American Reed Organ (Vestal, New York: Vestal Press, 1973), 18.
7. Ibid., 97–99. Gellerman’s list of stop names gives some indication of the diversity and lack of standardization among the American reed organ manufacturers.
8. The point of division between bass and treble was called the “split point.”
9. The harmonium did not employ the swell shade of the American system for dynamic contrast because the pressure system made possible quick changes in air speed. Quick control of air speed permits the execution of sharper accents and faster dynamic changes than is typically possible on the American instrument. Simply put, the American instrument is easier to learn how to play, but lacks the degree of potential interpretive refinement offered by the harmonium.
10. The phenomenon is due to inertia. Lowest reeds speak quite slowly: they are the largest reeds, sometimes several inches in length.
11. Gellerman, American Reed Organ, 107.
12. I have consistently used “American Reed Organ” or simply “reed organ” to refer to the suction bellows action design, and “harmonium” to describe the European pressure instrument.
13. Standardized pitch range, split point, sets of stop pulls, shared nomenclature. Nevertheless, as the 19th century progressed, European harmonium manufacturers (like their American counterparts) succumbed to the lure of increased capability that culminated with the celebrated “Art Harmonium.” The Art Harmonium offered a whole new range of attractive colors and capabilities. Music written for the Art Harmonium could not be played on more basic harmonium models.
14. Casey Pratt, e-mail to the author, July 30, 2013. Casey Pratt is a United States reed organ restorer who specializes in the Mason & Hamlin. Exact numbers are not known to date.
15. Ibid.
16. For instance, Liszt owned a piano-harmonium specially designed for him by Erard and Alexandre and a Chickering grand that was used in his piano master classes. He also collected then “antique” pianos that belonged to Mozart and Beethoven.
17. The Liszt Organ has a set of uniquely voiced, so-called “Liszt” reeds of great tonal beauty.
18. The main biographical information to date regarding Arthur Bird was amassed by Dr. William Cushing Loring (1914–2002). Loring was a Harvard graduate and an urban sociologist. After retirement, he focused on American art and music, working with Scarecrow Press to develop a series of more than twenty books on various North American composers.
19. Available at the International Music Score Library Project website: http://imslp.org.
20. Another likely reason piano sales surged ahead of the reed organ resulted from the installment purchase plans offered by piano companies. Once a luxury item of the upper classes, the piano then became affordable to the burgeoning middle class.
21. The flamboyant case styles of American reed organs clearly indicate a function beyond that of simply a musical instrument. In addition to ornate carvings, some reed organ cases featured a façade of non-functional organ “pipes,” mirrors, candle holders, and the like.
22. This information was communicated by Frans Vandergrijn, a Netherlands-based authority on reed organs and harmoniums in a posting on Yahoo’s Reed Organ Restoration newsgroup, August 9, 2013.
23. Pratt, e-mail to the author, August 10, 2013. To put these prices in perspective, average United States yearly income in 1900 was $438.
24. http://imslp.org/wiki/10_Pieces_for_Harmonium,_Op.37_(Bird,_Arthur_H.)
25. Modern recordings include music for piano 4-hands, op. 23, Vladimir and Nadia Zaitsev, pianists; Introduction and Fugue, op. 16, Tony and Mary Ann Lenti, pianists; Serenade for Wind Instruments, op. 40, Suite for Double Wind Quintet, op. 29 (Naxos), and Carnival Scenes for Orchestra, op. 5 (Albany).
26. William C. Loring, Jr., “Arthur Bird, American,” The Musical Quarterly 29:1, January 1943, 87.
27. Ibid., 88.
28. Ibid., 86.
29. Op. 37, 1897; op. 38, 1901; op. 39, 1903; op. 41, 1906; op. 42, 1905; op. 44, 1903; op. 45, 1905. All are available at the Library of Congress.
30. Not all of the op. 37 pieces scanned and available in IMSLP come from the original 1897 printing, several being from later editions. The only difference is that additional equivalent registration intended for European suction instruments was added.
31. My supposition is that Breitkopf titled them for the “American Harmonium” in order to alert purchasers that the intended instrument would be one of American design. European suction instruments could have been more or less acceptable alternatives, but only the Mason & Hamlin Normal-Harmonium would have had the subtle specificity of timbres and tonal balances characteristic of the Mason & Hamlin sound.
32. On IMSLP: http://javanese.imslp.info/files/imglnks/usimg/2/2d/IMSLP65232-PMLP1327…
33. See performance at http://www.youtube.com/watch?v=VIC9EwIjmks
34. And Percy Grainger’s later work for the reed organ.
35. See performance at http://www.youtube.com/watch?v=fi6yjMzjKe.
36. The American Reed Organ Society has been in existence since 1981.
References
Archival Sources
Music Division, Library of Congress, Washington, D. C. Music of Arthur Bird. Includes all his published music for reed organ, plus some manuscript scores.
Books and Articles
Brown, Andrea Elizabeth. “A Descriptive Analysis of Arthur Bird’s Suite in D.” DMA diss., University of North Carolina at Greensboro, 2010.
Elson, Louis C. American Music. New York, NY: MacMillan Co., 1904.
Gellerman, Robert F. The American Reed Organ. Vestal, NY: The Vestal Press, 1973.
———. The American Reed Organ and the Harmonium. Vestal, NY: The Vestal Press, 1996.
Good, Edwin M. Giraffes, Black Dragons, and Other Pianos. Stanford, CA: Stanford University Press, 2001.
Hendron, Michael, ed. Manufacturers Music Album Reed Organ Society Anthology Series. Palmer, Massachusetts: The Reed Organ Society Publications Office, 2001.
Hiles, John. A Catechism for the Harmonium. London: Brewer and Company, 1877.
Loring, William C., Jr. “Arthur Bird, American.” Musical Quarterly 29, no. 1 (1943): 78–91.
———. Arthur Bird: His Life and Music. Newton Centre, MA: n.p., 1941.
———. The Music of Arthur Bird: An Explanation of American Composers of the Eighties and Nineties for Bicentenial Americana Programming. Atlanta: n.p., 1974.
Milne, H. F. The Reed Organ: Its Design and Construction. Chancery Lane, England: Office of Musical Opinion, 1930.
Recordings
Bird, Arthur. Suite in D. On Bird Songs: Romantic Chamber Music of Arthur Bird, North Texas Chamber Players. Eugene Corporon, conductor. CD (digital disc). Klavier, KCD-11071, 1995.
———. Suite in D. On Collage: A Celebration of the 150th Anniversary of the Peabody Institute, 1857–2007. Peabody Conservatory Wind Ensemble. Harlan Parker, conductor. CD (digital disc). Naxos, 8.570403, 2008.
———. Suite in D. University of Cincinnati Chamber Players. Rodney Winther, conductor. CD (digital disc). Mark Records, 7212, 2007.
———. Amerikanische Weisen, op. 23, Three Characteristic Marches, op. 11, American Souvenirs Piano Music for Four Hands, Nadia and Vladimir Zaitsev, pianists, CD (digital disc), Gleur De Son-Qualiton/The Orchard, 57928, 2004.
Bird, Arthur; Dussek, Jan Ladislav; Liszt, Franz; Grieg, Edvard; and Onslow, George; Forgotten Piano Duets, Vol. 2, Tony and Mary Ann Lenti, pianists, CD (digital disc), ACA Digital Recording, B004QEZC2, 2011.