Matthew M. Bellocchio, a Project Manager and designer at Andover Organ since 2003, is a Fellow and past President of the American Institute of Organbuilders.
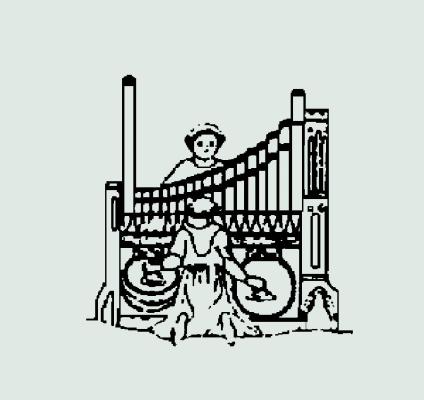
Andover Organ Company marks seventy years
by Matthew M. Bellocchio
Anniversaries invite us to reflect upon our past and contemplate how far we have come. As 2018 marks Andover Organ Company’s seventieth anniversary, this article will highlight its long and rich history, from its humble beginnings to its recent achievements.
Andover was founded in 1948 as a result of an Organ Institute organized by Arthur Howes, head of the organ department at the Peabody Conservatory, and held each summer on the campus of Phillips Academy in Andover, Massachusetts. Howes had traveled extensively in Europe and observed the developing Organ Reform Movement there. Originating in Germany in the 1930s from Albert Schweitzer’s writings, the movement sparked an interest in early music and performance practices, as well as the building of new organs that could authentically render early music, especially that of Bach. Howes started the Organ Institute to help spread the Organ Reform Movement in America. The faculty included such notable organists as Carl Weinrich (Princeton University), Ernest White (St. Mary the Virgin, New York City), and E. Power Biggs.
Tom Byers, a former Henry Pilcher’s Sons Organ Company employee who lived in nearby Lawrence, Massachusetts, attended the annual institute with his wife. He was inspired to start an organ company that would follow the institute’s philosophy. He chose the name “Andover” for its prestigious association with the Organ Institute and because of the advantages, in the pre-internet days of telephone directories, of appearing near the top of the alphabetical company listings.
Byers chose the opening line of Psalm 98, “Cantate Domino Canticum Novum” (Sing to the Lord a New Song), as the company motto, which still appears on Andover’s letterhead. This underscored his philosophy of creating a new style of organ, one that looked and sounded differently from what most American organ companies were producing.
Despite its name, the company has never been located in Andover! It started out in the home of Tom Byers in Lawrence, just north of Andover, and later moved to a two-story wooden building in nearby Methuen. In 1979 the company purchased a three-story brick building in a former mill complex at 560 Broadway in Lawrence, where it has been ever since.
Leadership and people
Rather than having a single leader dictate the company’s course, Andover’s many talented employees have each contributed to the company’s development. The company has always been owned and run by its principal employees who, serving as its shareholders and board of directors, make decisions collegially.
Charles Fisk joined the company in 1955 as Tom Byers’s junior partner. Robert J. Reich, a Yale-trained electrical engineer, was hired in 1956, and Leo Constantineau, a woodworking teacher and professional draftsman, in 1957. In 1958, Byers left the company, and Fisk became the owner. Walter Hawkes, who had worked for Holtkamp, was hired as shop foreman. Later that year, Andover signed a new organ contract with Redeemer Lutheran Church in Lawrence, Massachusetts. The contract did not specify the type of action. But the result, premiered on Palm Sunday 1959, was the first new mechanical-action organ built by an American firm in the postwar era. That instrument, Opus 28, is still in use.
The following year, Opus 35, a 33-stop tracker designed by Leo Constantineau and voiced by Charles Fisk, was built for Mount Calvary Episcopal Church in Baltimore, where Arthur Howes was organist. Fisk left Andover in 1961 to start his own company,
C. B. Fisk, in Gloucester, Massachusetts. Andover was reincorporated with Robert J. Reich and Leo Constantineau as the new owners. Reich, who became the Tonal Director, revised Andover’s pipe scales to provide more foundation tone. Constantineau’s case designs gave the company’s new instruments a distinctive visual flair.
Andover has been blessed with several dedicated individuals who each worked over fifty years at the company. Reich, who joined Andover in 1956, served as President and Tonal Director 1961–1997; he then worked part-time until retiring in 2009. Donald Olson joined the company in 1962 and became Andover’s general manager and visual designer in 1968. His elegant case designs were the hallmark of Andover’s new instruments for nearly four decades. He succeeded Robert Reich as President in 1997, stepped down in 2012 and then worked part-time until fully retiring in 2015. Robert C. Newton, who started at Andover in 1963 and headed the Old Organ Department for many years, retired in 2016.
Andover’s current President, Benjamin Mague, joined Andover in 1975. He holds a Bachelor of Arts degree in music from Colby College and a Master of Music degree in organ from the University of Wisconsin. He served as Andover’s mechanical designer and later as shop foreman before becoming President in 2012.
John Morlock, Andover’s Tonal Director since 1999, joined the company in 1976, working principally in the Old Organ Department. Don Glover, Andover’s in-house reed voicer, came to Andover in 2004 from the Reuter Organ Company.
Michael Eaton, Andover’s visual designer, joined the company in 1991. He also heads a maintenance team and serves as Treasurer and Clerk for Andover’s board of directors.
Andover’s present team of dedicated and talented people collectively possess over 350 years of organbuilding experience. Other current employees are Ryan Bartosiewicz, Matthew Bellocchio, Eric Dolch, Anne Doré, Andrew Hagberg, Lisa Lucius, Kevin Mathieu, Fay Morlock, Jonathan Ross, Craig Seaman, and David Zarges. Appropriately, more than half of Andover’s employees are church musicians or organists.
Andover has been the parent for many other New England tracker organ companies, having employed over its seventy years many talented individuals who later founded their own companies. These include Philip Beaudry, Timothy Fink, Charles Fisk, Timothy Hawkes, Richard Hedgebeth, Fritz Noack, Bradley Rule, J. C. Taylor, and David Wallace.
Tonal style
Tonally, the early Andover organs were inspired by the Organ Reform Movement. At the time of Andover’s founding, few American companies were repairing old tracker organs; most just electrified or replaced them. Andover was the first to deliberately retain and renovate nineteenth-century trackers. But, adhering to the Organ Reform philosophy, Byers and his early successors often “improved” those organs tonally. It was not unusual for them to evict the string stops and replace them with mixtures and mutations. Andover’s new instruments came to be characterized by strong Principal choruses with bright mixtures, colorful neo-Baroque style flutes and mutations, and reeds that emphasized chorus over color.
In the 1980s, as Andover began more frequently to work on significant nineteenth-century American organs, a gradual transition occurred. This was solidified in 1999 when John Morlock, who had started in Andover’s Old Organ Department, succeeded Robert Reich as Tonal Director.
Today, Andover’s tonal style may best be described as “American” and is grounded primarily in the best practices of the nineteenth-century New England builders, in particular the Boston firm of E. & G. G. Hook. Their organs, especially those from the firm’s “golden period” (1850s to 1870s), are admired for their remarkably successful blend of warmth and brilliance. Their pipe scales and voicing techniques worked extremely well in the dry acoustics of many American churches.
When designing a new organ or reworking an existing instrument, we basically use the same scaling proportions between the various stops of the chorus that the Hooks used. We have found that doing so results in a principal chorus that is nicely balanced between fundamental weight and harmonic development.
Within this framework, adjustments are made to reflect or, in some cases, compensate for the acoustical properties found in each room. Each instrument needs to work and sound well in its “home” and be able to perform its tasks capably and effectively. Andover organs are designed to lead and support congregational hymn singing, as well as interpret a wide range of organ literature.
Maintenance
From the very beginning, organ maintenance was an important part of the company’s work. It created name recognition, established relationships with churches and organists, and provided a consistent revenue stream. Today, Andover maintains over 300 organs annually throughout the Northeast, Mid-Atlantic, and Southeast—from northern Maine to South Carolina, from western New York to the islands off eastern Massachusetts. These instruments range in size from small one-manual trackers in country churches to the world-famous Great Organ (IV/116) in the Methuen Memorial Music Hall; and range in age from a few years to a historic 1762 Snetzler organ.
We service all types of organ mechanisms—from traditional tracker action to modern solid-state relays and combination actions. Each spring and fall, we schedule extended maintenance tours to visit multiple instruments in a geographical area. This enables our customers to share the travel expenses.
Many customers treat us like old friends. Occasionally, a church secretary or organist will call us and merely say, “This is so-and-so at First Parish Church,” not realizing that we have over three dozen tuning customers with that name!
Andover Organ firsts
As the leader in the mid-twentieth century tracker organ revival in America, Andover pioneered many innovations that are now standard in the industry. Opus 25, a two-manual built in 1958 for the Rice Institute (now University) in Houston, was an electro-pneumatic instrument utilizing slider chests with pneumatic pallets, one of the first examples of this pallet type. This was decades before the adoption of the “Blackinton-style” pneumatic pallet.
In 1961, Andover carried out the first historically sympathetic restoration of a nineteenth-century American organ: the 1-manual, 1865 E. & G. G. Hook Opus 358 at the Congregational Church in Orwell, Vermont (Andover Opus R-1.)
Other significant Andover (AOC) restorations include:
• First Presbyterian Church, Newburyport, Massachusetts (1866 E. & G. G. Hook/AOC 1974);
• First Parish Church, Bridgewater, Massachusetts (1852 E. & G. G. Hook/AOC 1977);
• South Parish Congregational Church, Augusta, Maine (1866 E. & G. G. Hook/AOC 1982);
• Church on the Hill, Lenox, Massachusetts (1869 William A. Johnson/AOC 2001);
• Old Whaling Church, Edgartown, Massachusetts (1850 Simmons & Fisher/AOC 2004);
• Centre Street Methodist Church, Nantucket, Massachusetts (1831 Thomas Appleton/AOC 2008);
• St. Peter’s Catholic Church, Haverstraw, New York (1898 Geo. Jardine & Son/AOC 2011);
• St. Anna’s Chapel, Newburyport, Massachusetts (1863 William Stevens/AOC 2013).
Utilizing its expertise gained from restoring old tracker organs and building new ones, in 1963 Andover was the first company in the world to re-trackerize an old tracker organ that had been electrified. The instrument was the 1898 James Treat Opus 3 at St. George’s Primitive Methodist Church (now Bethesda Missionary Church) in Methuen, Massachusetts.
Other notable re-trackerizations:
• First Presbyterian Church, Waynesboro, Virginia (1893 Woodberry & Harris/AOC 1986);
• St. John’s Episcopal Cathedral, Providence, Rhode Island (1851 E. & G. G. Hook/AOC 1989);
• Westminster Preservation Trust, Baltimore, Maryland (1882 Johnson & Son/AOC 1991);
• Sage Chapel, Northfield, Massachusetts (1898 Hook & Hastings/AOC 1996);
• Unitarian Society, Peterboro, New Hampshire (1867 E. & G. G. Hook/AOC 2003);
• Christ Episcopal Church, Charlottesville, Virginia (1869 E. & G. G. Hook/AOC 2012).
The slider and pallet windchests used in most nineteenth-century organs were generally trouble free for many years. However, when heating systems were introduced into churches in the early twentieth century, problems developed. The solid wood chest tops (tables), just below the sliders, were made from a thin, wide plank of air-dried lumber. With constant heating the wooden tables dried out and cracked, allowing air to leak from one pipe hole to the next, resulting in “runs.”
Andover was the first American company to replace a cracked, solid-wood table with a marine-grade plywood one. The routed bleed channels between the table’s wind holes were then carefully replicated and the entire table graphited, like the original. This type of table replacement is now standard in the industry. The first organ to receive this treatment, in 1965, was the 1897 George W. Reed, at the Baptist Church in Winchendon, Massachusetts. Sadly, the organ burned with the building in 1985.
One of Andover’s most significant recent projects was the 2016 restoration of the wind system and key action in the 1892 Woodberry & Harris Opus 100 at St. Mary–St. Catherine of Sienna Parish in Charlestown, Massachusetts. With three manuals, 36 stops, and 41 ranks, it is the largest and most significant nineteenth-century organ remaining in original unaltered condition in the greater Boston area.
The instrument’s action is entirely mechanical and incredibly complex. The three-manual, reversed detached console sits in the center of the gallery, while the pipes and windchests are in cases at either side of a large stained-glass window. Four levels of trackers descend from the keys to squares beneath the floor, then under the console towards the rear window, then turn off at right angles towards the sides, then turn off again at right angles towards the rear, then to squares which send them up to the rollerboards below the chests. The organ’s four divisions have a total of 17 sets of wooden trackers, totaling nearly a mile in length! A Barker machine lightens the touch of the Great and the manuals coupled to it.
The two large reservoirs were stripped and releathered in place. All four layers of trackers were disassembled, labeled, and brought to the shop for replication. Because of the organ’s historic significance, all the new trackers were made of the same materials as the originals but using modern machinery. Andover customized a miniature CNC router to notch the cloth-wrapped tracker ends and built a spinning machine to whip the threaded wire ends with red linen thread, just like the originals. The Barker machine was carefully releathered. “Now she runs like a Bentley,” said one of the instrument’s many admirers.
Rebuilding for reliability
A conservative restoration is the logical decision for an exemplary work by an important builder or a small organ in a rural church with modest musical requirements. But sometimes it is necessary to strike a balance between preserving the original fabric and updating it to suit modern needs. An organ that has already endured several unsympathetic rebuilds, or an aging instrument with unreliable mechanisms and limited tonal resources, in an active church or institution with an ambitious music program might be better served by a sympathetic rebuilding. This was the case with two of Andover’s most significant rebuilds.
The 1876 E. & G. G. Hook & Hastings Opus 828 at St. Joseph Cathedral in Buffalo, New York, was built as a showpiece for the 1876 “Centennial Exposition” in Philadelphia and purchased afterwards by the cathedral. Major changes were made to the organ by Tellers-Kent Organ Company in 1925 and by Schlicker Organ Company in 1976. By 1996, the organ was virtually unplayable during the winter months and a decision of whether to replace it or rebuild it was imminent. In 1998, the cathedral decided that “the organ need not be replaced, but rather completely rehabilitated.” At the same time, the organ’s tonal palette needed expanding to better serve the musical needs of the cathedral and to enable it for use in concerts and recitals.
A team from Andover dismantled the organ in July 1999, loaded it into two moving vans, and transported it back to Lawrence, where eighteen employees labored for more than a year to clean, repair, and expand the instrument. In undertaking this immense job, Andover sought to retain and restore as much of the original as possible. The entire organ was cleaned, and the black walnut case stripped of coats of dark varnish and restored to its original finish. The façade pipes were stripped and repainted in their original designs with colors that harmonized with the cathedral’s interior.
All the original chests and pipework were rebuilt and repaired. The manuals were expanded to 61 notes and the pedals to 32. The two original reservoirs were releathered and two new ones constructed. The Choir is now unenclosed, as it originally was, the Swell box is back to its original size, and the Solo is restored to its original position.
Many of the missing original pipes were replaced with pipes salvaged from the Hook 1877 Cincinnati Music Hall organ, Opus 869. Other compatible Hook organs were visited to develop pipe scales appropriate for the additions to the cathedral organ, which were voiced in the Hook style. The organ is now far closer to its original sound than it has been since the 1923 electrification and rebuilding.
A new floating Celestial Division on a slider windchest was added. This division was based on contemporary E. & G. G. Hook solo divisions, as typified by the organs in the Cincinnati Music Hall and Mechanics Hall, Worcester. There is an 8′ Philomela copied from the 1863 Hook at Church of the Immaculate Conception in Boston, an original Hook 4′ Hohlpfeife, a 2′ Harmonic Piccolo, a Cor Anglais, and a few more modern stops stops such as a French Horn, Dolcan Gamba with Gamba Céleste, Spitzflöte and Spitzflöte Céleste.
Thomas Murray played the rededicatory recital on June 11, 2001. The St. Joseph Cathedral organ will be featured in a recital by Nathan Laube during the American Guild of Organists Northeast Regional Convention, July 1–4, 2019.
In contrast to the Buffalo cathedral organ, the 1902 Hook & Hastings Opus 1833 at St. John’s Seminary in Brighton, Massachusetts, was a modest two-manual, 18-rank instrument. After nearly a century of use and constant winter heating, the windchests and actions developed serious problems. The original console was replaced in 1946. When the replacement console failed in 2004, a one-manual tracker was put in its place to serve as a temporary instrument until the chapel organ could be rebuilt.
Our lengthy experience with Hook & Hastings organs taught us that their early electro-pneumatic actions were cumbersome, slow, and difficult to repair. Therefore, in our 2014–2015 rebuilding of the organ, we reused the pipes, windchests, and most of the original parts as the basis of an expanded instrument with a new electric action.
We built a new, solid white oak console in the style of the Hook & Hastings original, with a lyre music rack and elliptically curved stop terraces. To meet the demands of a twenty-first century music program, this reproduction console has state-of-the-art components, including a record/playback module. The façade pipes were stripped and repainted with a new decorative treatment that harmonizes with the Italian Renaissance-style case and chapel. As a crowning flourish, the cross surmounting the case was painted in faux lapis lazuli.
Most of the organ was crammed within the small case, with Swell above Great and the wooden Pedal 16′ Open Diapason pipes at each side. Behind the Swell, in an unfinished gallery, were the organ’s large reservoir and Pedal 16′ Bourdon. We moved the Pedal Open Diapason pipes to the rear gallery and added a Pedal 32′-16′-8′ Trombone and 8′-4′ Principal there. Judicious additions to the Swell expanded its resources. There was sufficient space inside the case behind the Great chest to add a seven-stop unenclosed Choir division.
The end result of these tonal changes and additions is an instrument of 40 stops, 34 ranks, and 1,994 pipes that is more versatile and appropriate for its expanded role. It still sounds very much like a Hook & Hastings organ, but one from an earlier and better period of the firm’s output.
Façade firsts
The company’s work with historic organs gradually led to pipe façade restorations as well. In 1967, Andover was the first American company to make restorative paint repairs to a painted and stenciled pipe façade, at the First Congregational Church in Georgetown, Massachusetts (1874 Joel Butler). Thirteen years later, in 1979, during its rebuilding of the 1884 Geo. S. Hutchings Opus 135 at the Vermont College of Fine Arts in Montpelier, Vermont, Andover carefully stripped a coating of green paint from all the façade pipes, documented the original designs and colors underneath, and repainted the pipes in their original colors and stenciling—another first.
Andover’s Opus 102 (1992) at Trinity United Church of Christ in York, Pennsylvania, was the first new American organ in the modern era to feature painted façade pipes with nineteenth-century style colored bandings. The upper façade flats of this organ contained another first: “frosted tin” pipes, which feature the natural, unplaned finish of the cast tin sheets. This gives them the light color of tin, but with a dull, non-reflective finish.
In recent years, Andover has worked with historic painted decoration conservator Marylou Davis to create new painted-pipe decorations in historically inspired styles. The most notable example of this collaboration is the 82-rank Andover Opus 114 (2007) at Christ Lutheran Church in Baltimore. This was the first twenty-first century American organ façade to combine polychromed and monochrome texture-stenciled pipes, frosted tin pipes, and numerous hand-carved pipe shades, grilles, finials, and skirtings in the casework.
Opus 114 is also Andover’s first dual-action, double organ. The 13-rank, electric-action gallery organ can be played from its own console or from the front organ’s three-manual mechanical-action console. Likewise, the entire front organ can be played from the two-manual gallery console through couplers and general pistons. The organ’s four matching cases (two in chancel, two in gallery) perfectly suit the church’s Gothic architecture and fool many people into thinking that they were reused from a 19th-century organ.
Andover has never been afraid to fit an organ around a prominent window. This reflects our design philosophy that an organ should look as if it has always been part of its environment. And in most churches, the window was there long before the organ. Fighting the window can sometimes be a losing battle. Opus 115 (2007) at Church of the Nativity in Raleigh, North Carolina, and Opus 118 (2014) at First Parish Church in Wayland, Massachusetts, illustrate Andover’s creative approach in dealing with windows.
In Raleigh, the modern clear glass window was front and center, at the top of the space where the organ would go. We designed the organ case to frame the window’s central orb and cross. The polished tin façade pipes match the brightness from the window. The organ also serves as a reredos for the altar, which stands in front of it. Looking from top to bottom, one sees the window, the organ, and the altar—light, music, action. The church was very pleased with the result, as were we.
In the 1820 Federal Period meetinghouse in Wayland, there was an elegant Palladian window in the center of the back wall of the rear gallery. Because of the semi-elliptical curve of the gallery’s rear wall, the only apparent organ placement with such a floor plan was in the center. Thus, all the previous organs had blocked the window. Andover’s design put the detached console in the center, by the railing, and divided the organ into two cases that frame, rather than cover, the Palladian window. The choir members sit in the space between the console and cases and benefit from the natural backlighting provided by the window. Again, everyone was pleased with the results.
Seventy years after its humble beginnings, Andover has much to celebrate: 118 new organs and 533 rebuilds/restorations. Andover’s wide-ranging work in building, rebuilding, restoring, and maintaining pipe organs is well-recognized, and best summarized by its mission statement: “Preserving the Past; Enhancing the Present; Inspiring the Future.”